Specialist Suggestions on What is Porosity in Welding and Just How to Resolve It
Specialist Suggestions on What is Porosity in Welding and Just How to Resolve It
Blog Article
The Scientific Research Behind Porosity: A Comprehensive Overview for Welders and Fabricators
Comprehending the intricate mechanisms behind porosity in welding is critical for welders and producers pursuing impeccable craftsmanship. As metalworkers look into the depths of this sensation, they uncover a world controlled by numerous variables that influence the formation of these minuscule spaces within welds. From the composition of the base products to the details of the welding procedure itself, a multitude of variables conspire to either exacerbate or relieve the existence of porosity. In this detailed overview, we will unravel the science behind porosity, exploring its results on weld top quality and unveiling advanced strategies for its control. Join us on this trip through the microcosm of welding flaws, where precision satisfies understanding in the pursuit of remarkable welds.
Understanding Porosity in Welding
FIRST SENTENCE:
Evaluation of porosity in welding discloses important understandings into the stability and top quality of the weld joint. Porosity, characterized by the existence of dental caries or spaces within the weld steel, is a typical concern in welding processes. These gaps, if not appropriately addressed, can jeopardize the structural honesty and mechanical properties of the weld, causing prospective failings in the finished product.
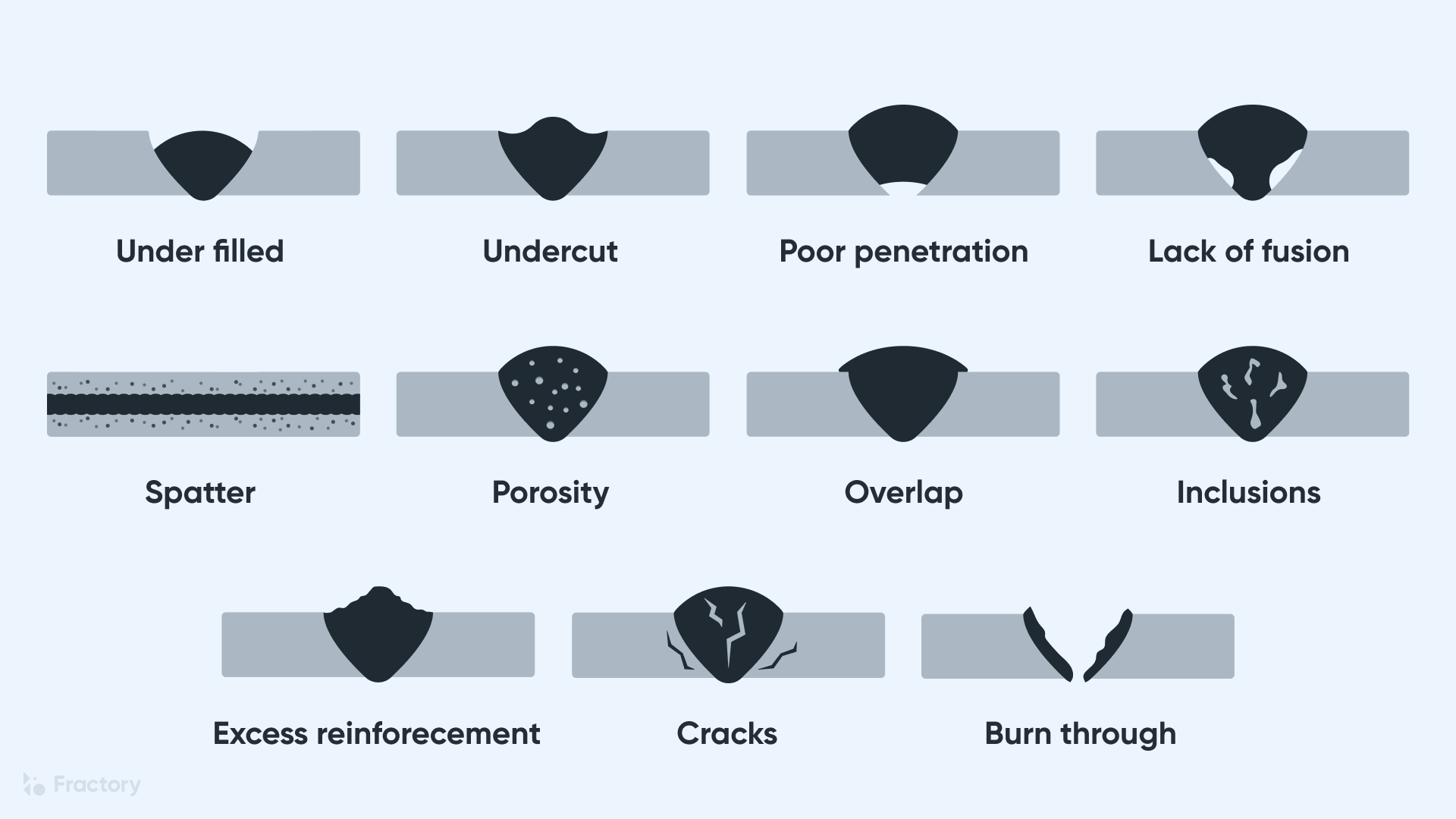
To discover and quantify porosity, non-destructive testing methods such as ultrasonic testing or X-ray examination are often employed. These techniques allow for the identification of interior issues without compromising the stability of the weld. By examining the size, form, and circulation of porosity within a weld, welders can make enlightened choices to enhance their welding processes and attain sounder weld joints.
Factors Affecting Porosity Formation
The event of porosity in welding is influenced by a myriad of elements, varying from gas securing efficiency to the intricacies of welding criterion setups. Welding specifications, including voltage, present, take a trip speed, and electrode kind, additionally impact porosity formation. The welding strategy used, such as gas steel arc welding (GMAW) or shielded steel arc welding (SMAW), can affect porosity formation due to variations in warm circulation and gas coverage - What is Porosity.
Effects of Porosity on Weld Top Quality
The presence of porosity also weakens the weld's resistance to corrosion, as the caught air or gases within the spaces can react with the surrounding environment, leading to deterioration over time. Additionally, porosity can prevent the weld's ability to withstand pressure or influence, more jeopardizing the general high quality and dependability of the welded structure. In critical applications such as aerospace, auto, look at here or architectural building and constructions, where safety and longevity are extremely important, the destructive effects of porosity on weld quality can have serious consequences, emphasizing the relevance of lessening porosity through appropriate welding strategies and procedures.
Strategies to Decrease Porosity
To improve the high quality of bonded joints and guarantee architectural integrity, welders and fabricators use particular methods targeted at reducing the formation of voids and dental caries within the material throughout the welding process. One reliable approach to decrease porosity is to guarantee correct product prep work. This includes complete cleaning of the base steel to eliminate any pollutants such as oil, grease, or dampness that can contribute to porosity development. Additionally, making use of the ideal welding criteria, such as anonymous the correct voltage, present, and travel speed, is essential in preventing porosity. Preserving a regular arc length and angle during welding likewise helps in reducing the chance of porosity.

Utilizing the appropriate welding method, such as back-stepping or utilizing a weaving movement, can also assist disperse warmth evenly see and reduce the opportunities of porosity development. By carrying out these methods, welders can effectively decrease porosity and create premium welded joints.

Advanced Solutions for Porosity Control
Executing cutting-edge innovations and ingenious techniques plays a crucial role in attaining exceptional control over porosity in welding processes. In addition, utilizing sophisticated welding methods such as pulsed MIG welding or modified environment welding can additionally help reduce porosity problems.
An additional advanced solution includes making use of innovative welding tools. Utilizing devices with integrated attributes like waveform control and advanced power sources can improve weld high quality and minimize porosity dangers. Additionally, the application of automated welding systems with exact control over criteria can considerably minimize porosity defects.
In addition, integrating sophisticated monitoring and inspection technologies such as real-time X-ray imaging or automated ultrasonic testing can aid in spotting porosity early in the welding process, enabling prompt rehabilitative activities. Generally, integrating these sophisticated remedies can greatly improve porosity control and enhance the general top quality of welded components.
Verdict
In final thought, comprehending the scientific research behind porosity in welding is necessary for welders and fabricators to generate top quality welds - What is Porosity. Advanced remedies for porosity control can better improve the welding procedure and ensure a solid and reliable weld.
Report this page